jimbo486
New member
Finished assembling the remaining 3 rocker lever assemblies. Bolted on the oil cooler and filter head package and the water inlet connection.
Set the head on the block and dropped in Hamilton's HD push rods, threaded in the ARP CA625 studs. Ran them in until hand tight as per their instructions.
Something didn't look quite right with the shorties between the exhaust runners. But the head wasn't seated just yet so I waited.
Sure enough...
I did notice that while bottom tapping the bores, the 6 along the exhaust side were about 3/8" deeper than the rest of the bores. I started to think that maybe those didn't need to be tapped. But, after counting 14 threads on the stud and 14 turns until it stopped in the bore, that tells me that all of the threads wouldn't have been engaged if I hadn't tapped them deeper.
Some guys I've talked to said to back them out until they're flush or that ARP says to back them out 1/4 of a turn. None can provide an official ARP document stating to back these studs out 1/4 of a turn and the instructions found on their website and that came with the studs do not say anything about backing them out. Only stating to run them in hand tight only. Nothing more. I ain't about to back them out because then it would be as if I didn't bottom tap and therefore, all of the threads again would not be fully engaged. Is this common for the early 12 valve blocks?
I measured one of the studs I took out with my calipers, 3.424". It appears they need to be 3/8-1/2" longer. Does anyone happen to have a 625+ set for a 12v and be willing measure the short stud for me? Kit #247-4205.
I'm gonna call ARP tomorrow and ask what happened. Before I go any further, I need to ensure that I can get the head seated fully before starting the torque sequence. I don't want to pull the head down with the studs.
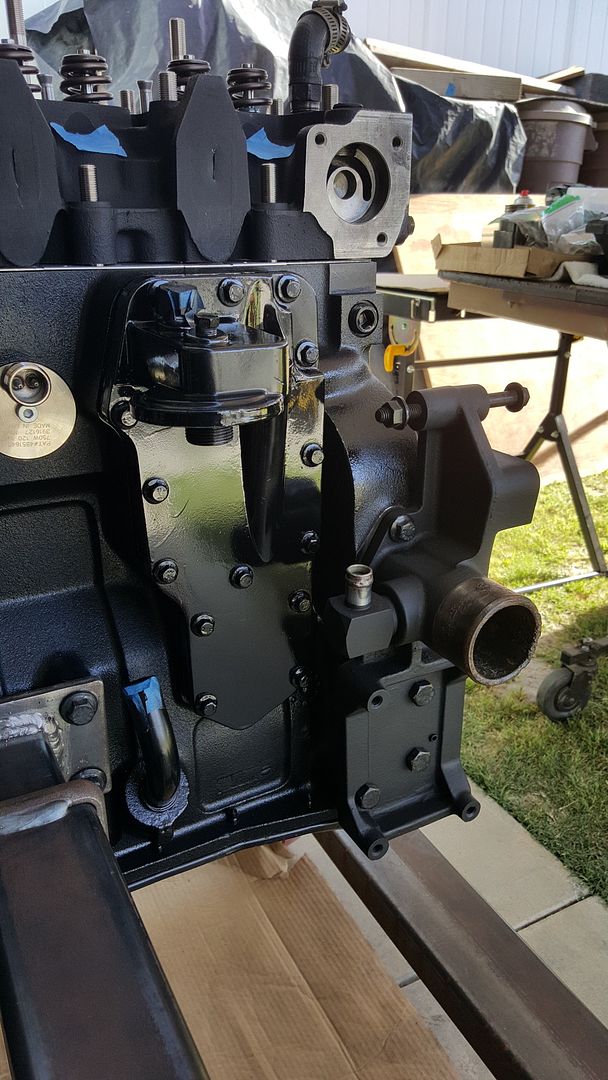
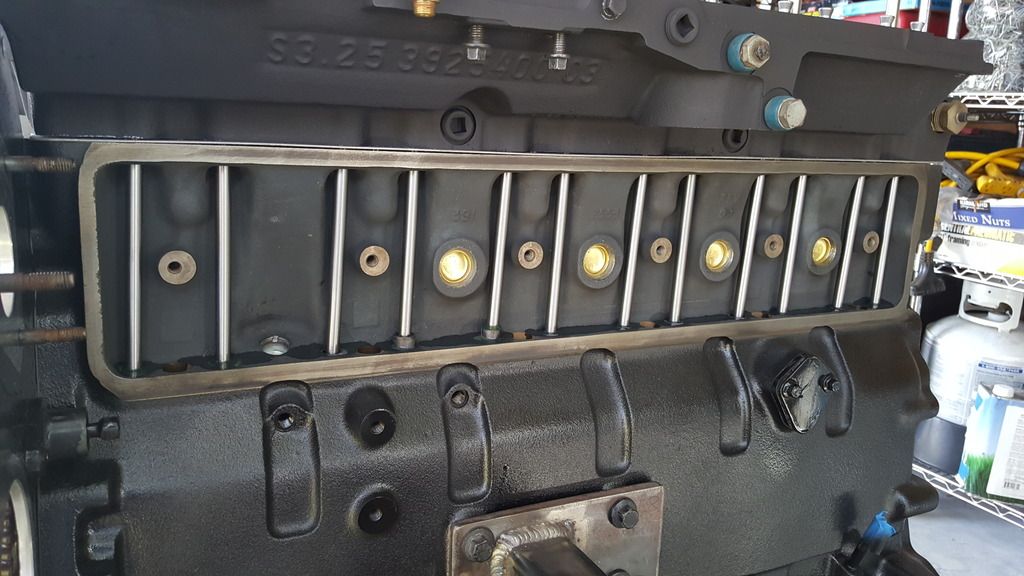
Set the head on the block and dropped in Hamilton's HD push rods, threaded in the ARP CA625 studs. Ran them in until hand tight as per their instructions.
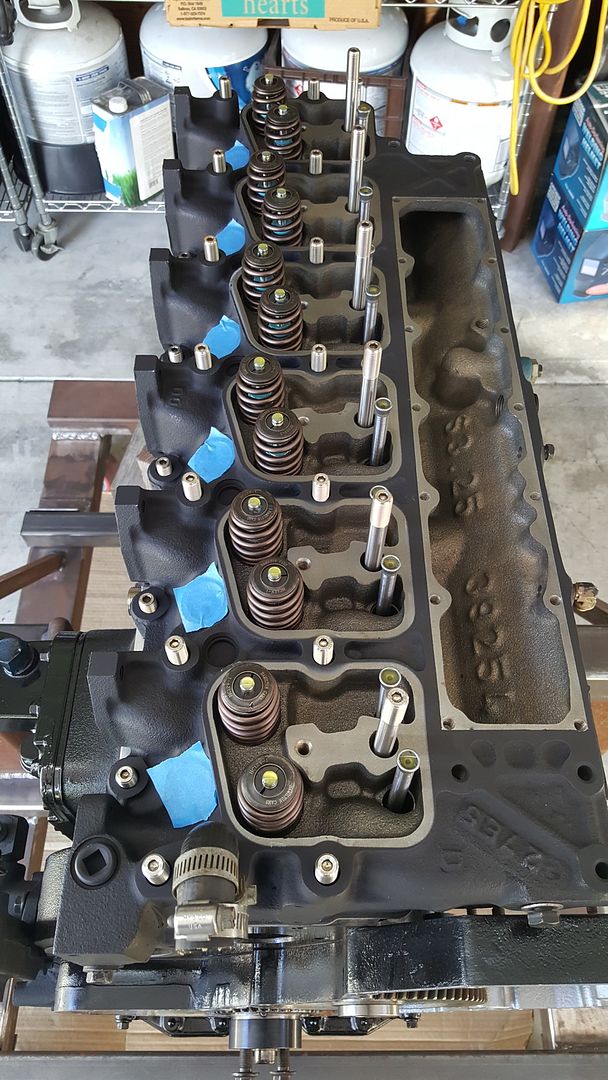
Something didn't look quite right with the shorties between the exhaust runners. But the head wasn't seated just yet so I waited.
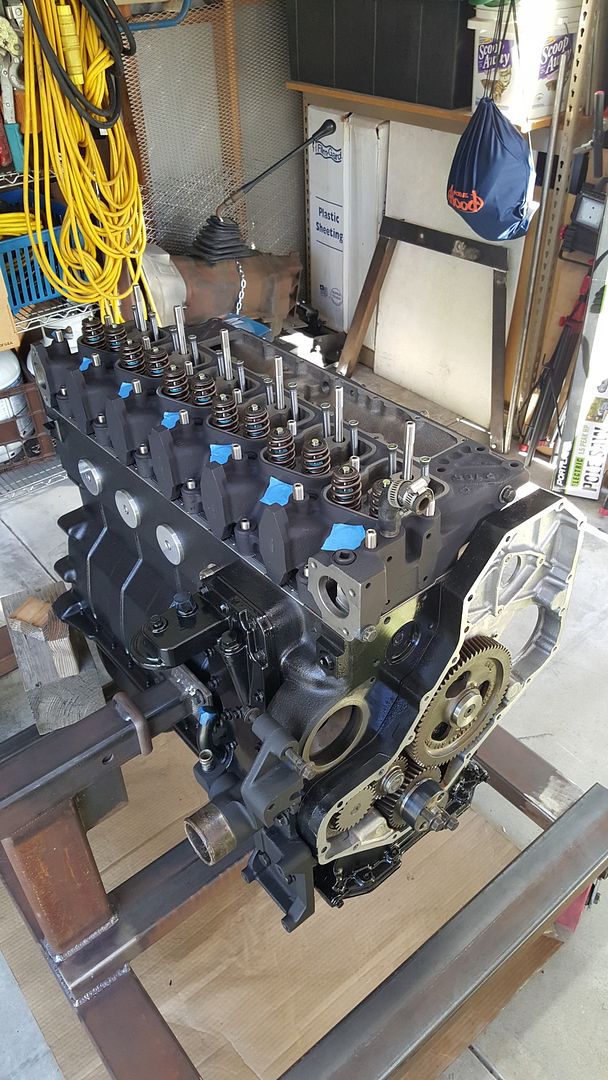
Sure enough...
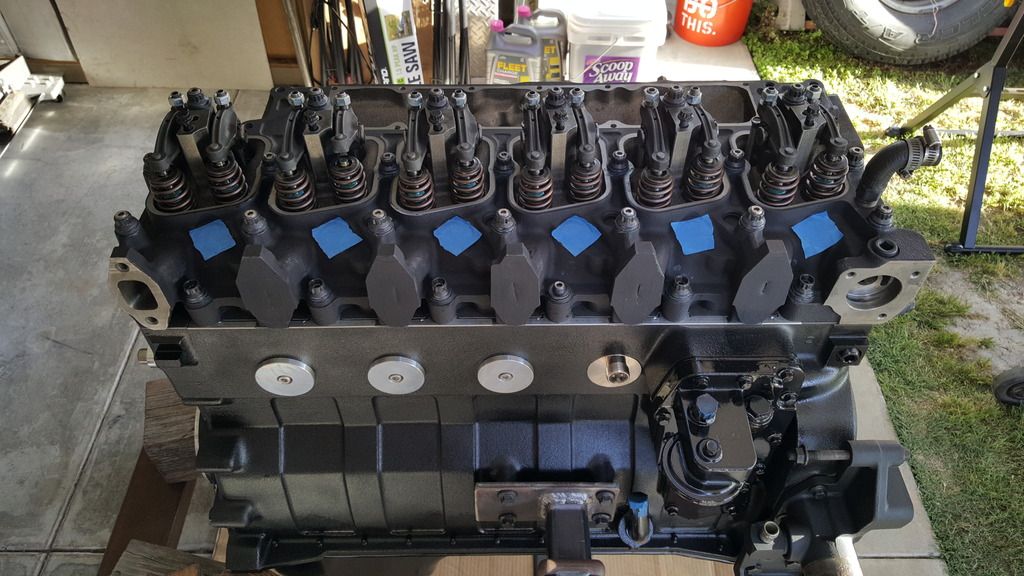
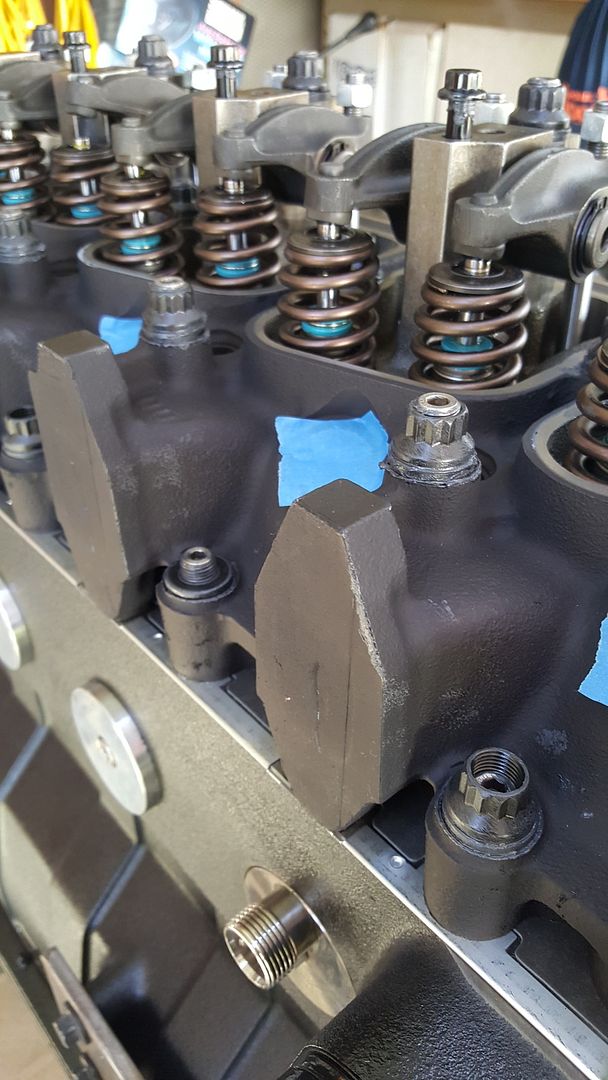
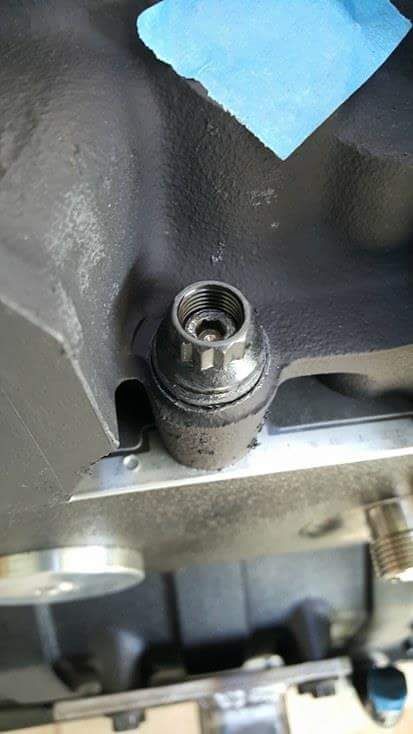
I did notice that while bottom tapping the bores, the 6 along the exhaust side were about 3/8" deeper than the rest of the bores. I started to think that maybe those didn't need to be tapped. But, after counting 14 threads on the stud and 14 turns until it stopped in the bore, that tells me that all of the threads wouldn't have been engaged if I hadn't tapped them deeper.
Some guys I've talked to said to back them out until they're flush or that ARP says to back them out 1/4 of a turn. None can provide an official ARP document stating to back these studs out 1/4 of a turn and the instructions found on their website and that came with the studs do not say anything about backing them out. Only stating to run them in hand tight only. Nothing more. I ain't about to back them out because then it would be as if I didn't bottom tap and therefore, all of the threads again would not be fully engaged. Is this common for the early 12 valve blocks?
I measured one of the studs I took out with my calipers, 3.424". It appears they need to be 3/8-1/2" longer. Does anyone happen to have a 625+ set for a 12v and be willing measure the short stud for me? Kit #247-4205.
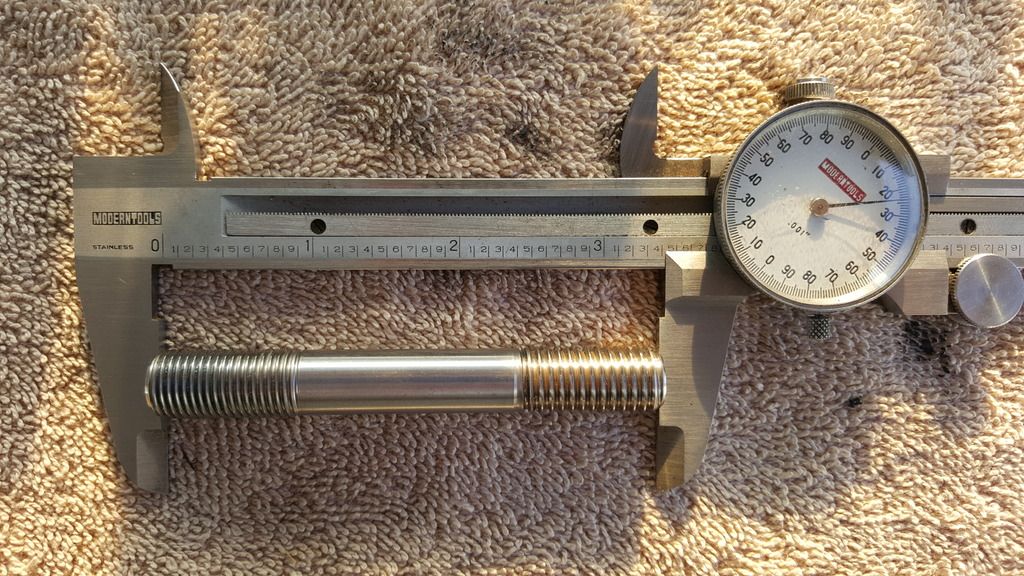
I'm gonna call ARP tomorrow and ask what happened. Before I go any further, I need to ensure that I can get the head seated fully before starting the torque sequence. I don't want to pull the head down with the studs.
Last edited: