jimbo486
New member
After building the stand/cart, I've been working on disassembly of my engine for the past few days. From what I can see, the head gasket didn't fail from excess boost pressure or advanced timing. It appears to be just a failure from a coolant passage seal next to cylinder #5 on the exhaust side.
Between #5 and #6 is where the leak made itself known.
The suspected coolant passage next to #5.
Block or bottom side of the gasket. It looks as though the coolant pushed out towards the cylinder and followed the fire ring around before going external below the exhaust runner. I guess some of the seal material missing would explain why I've occasionally seen small orange flakes in the coolant in the overflow bottle.
Flywheel, clutch disc and pressure plate assemblies removed along with the transmission adapter.
Strange finding the rear main seal with some pieces missing. However, it didn't leak. What could be the reason? Simply heat cycles from the engine caused the rubber to get brittle and break away? I installed this seal back in 2010 when the South Bend clutch went in. I used the supplied driver and had no issues during installation.
While not the proper way to check piston protrusion but it gives an estimate. Hamilton says for their cams to be truly bolt-in, piston protrusion cannot exceed .018". Since I don't have the dial gauge for checking protrusion, I'll lay a straight edge across the piston crown and check protrusion with feeler gauges to get a closer estimate.
Between #5 and #6 is where the leak made itself known.
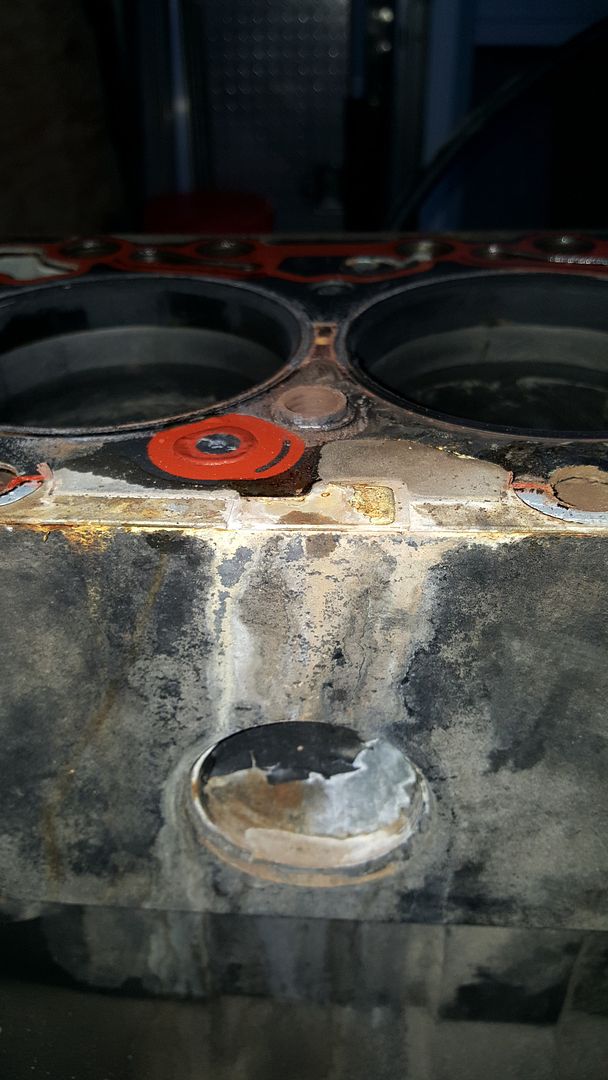
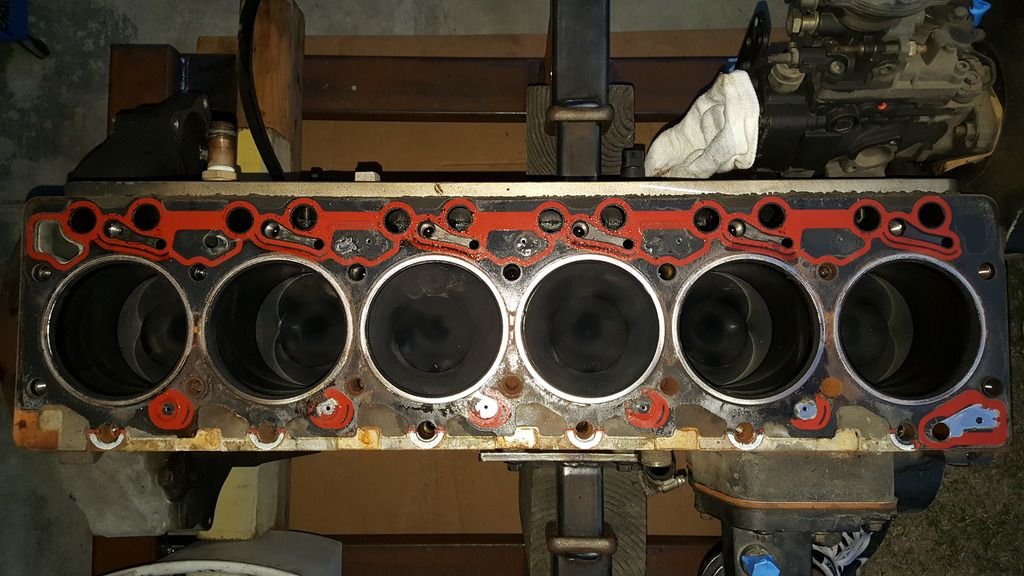
The suspected coolant passage next to #5.
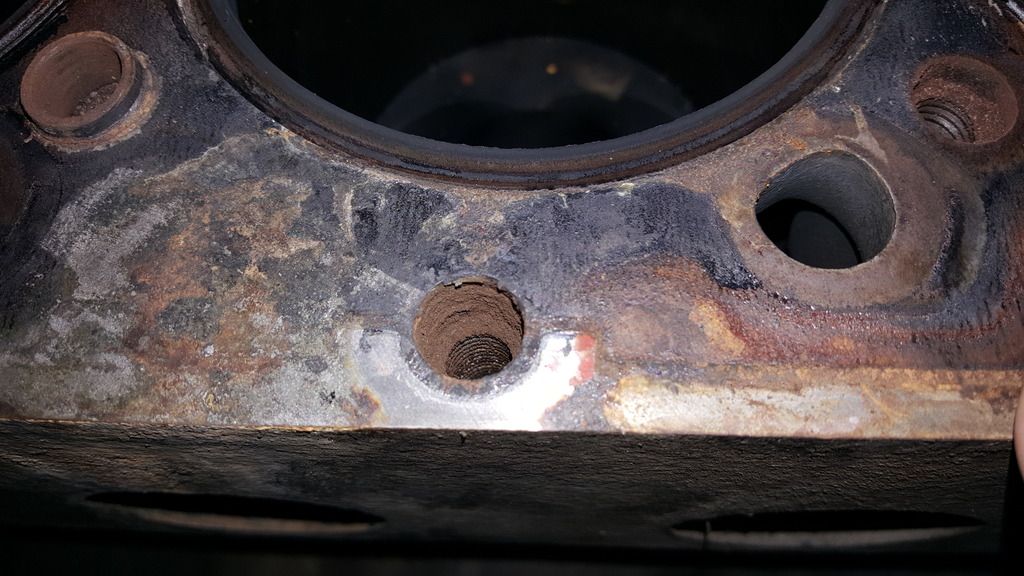
Block or bottom side of the gasket. It looks as though the coolant pushed out towards the cylinder and followed the fire ring around before going external below the exhaust runner. I guess some of the seal material missing would explain why I've occasionally seen small orange flakes in the coolant in the overflow bottle.
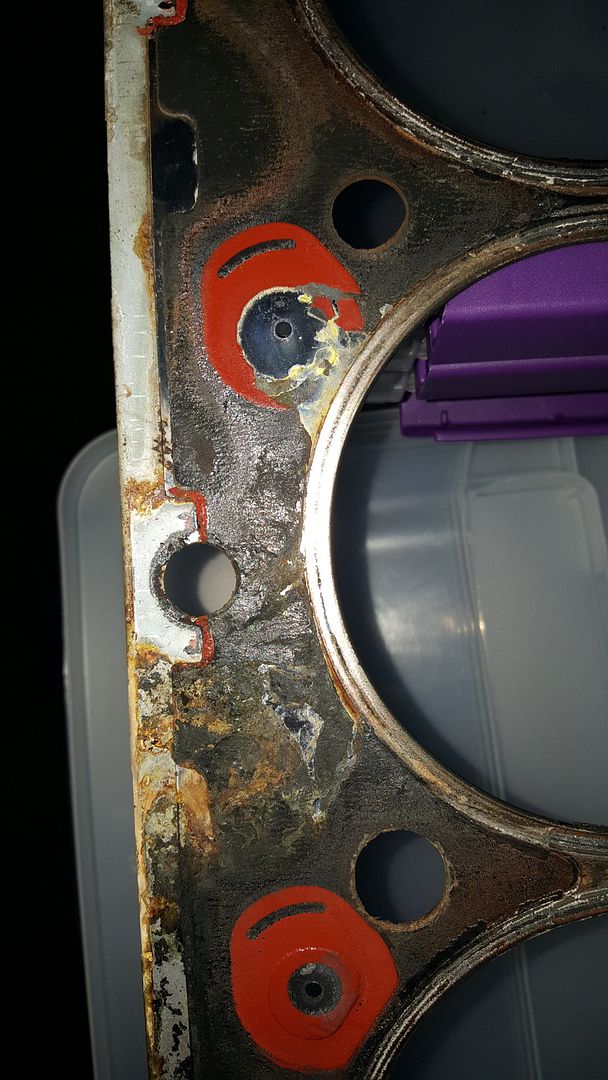
Flywheel, clutch disc and pressure plate assemblies removed along with the transmission adapter.
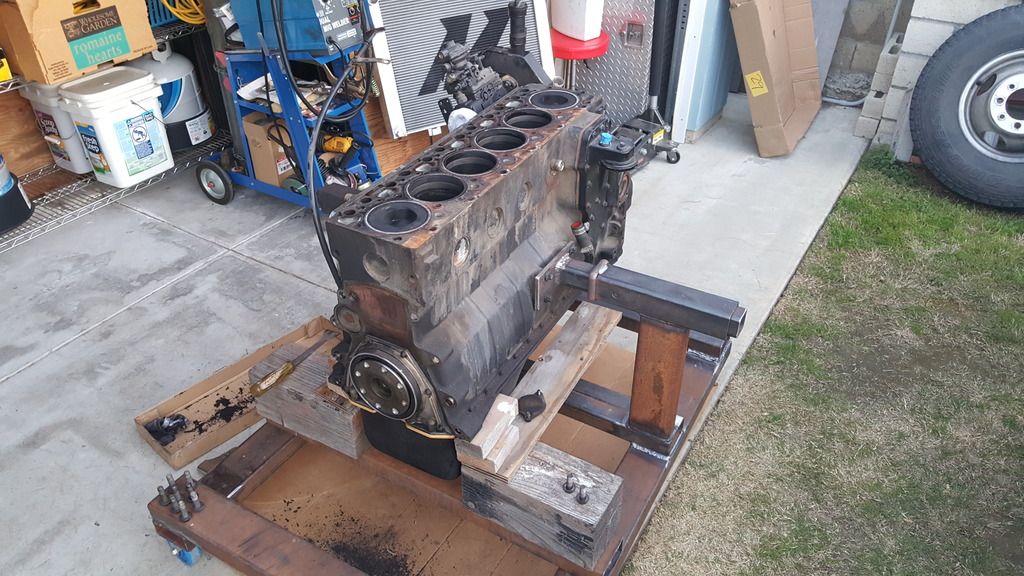
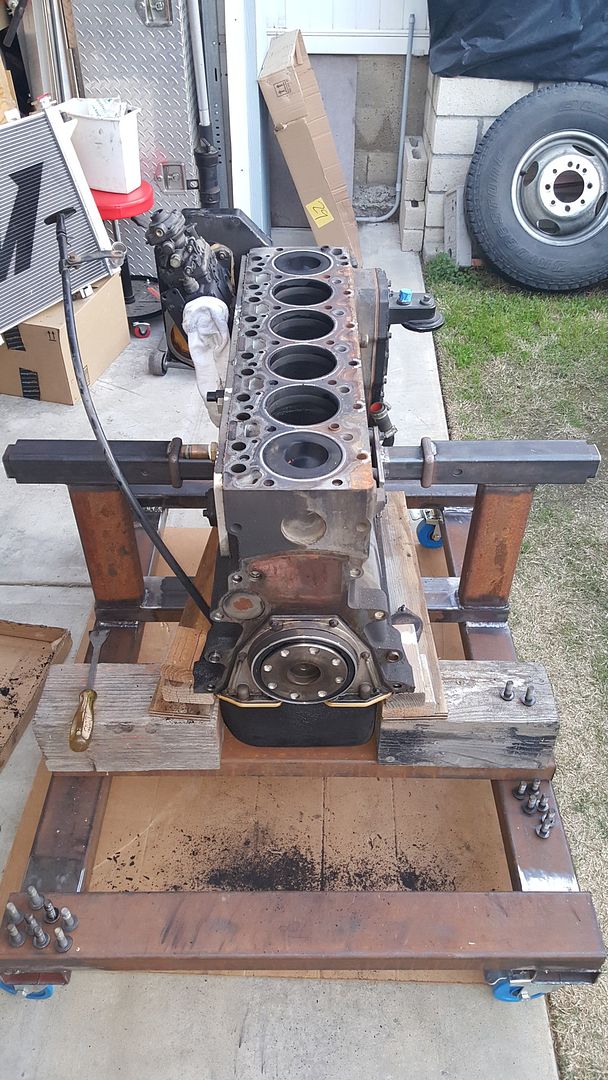
Strange finding the rear main seal with some pieces missing. However, it didn't leak. What could be the reason? Simply heat cycles from the engine caused the rubber to get brittle and break away? I installed this seal back in 2010 when the South Bend clutch went in. I used the supplied driver and had no issues during installation.
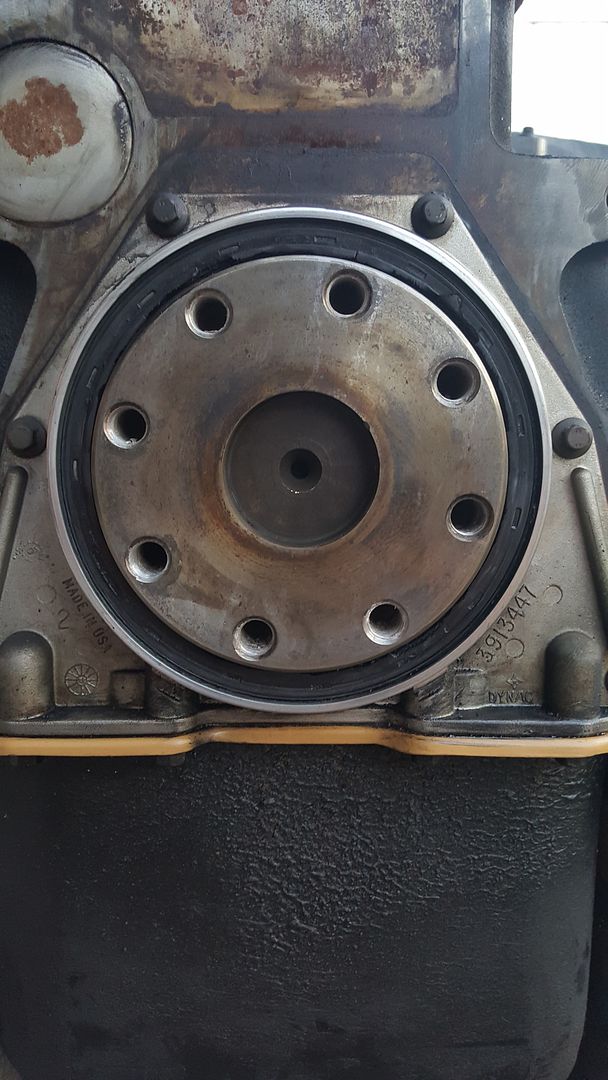
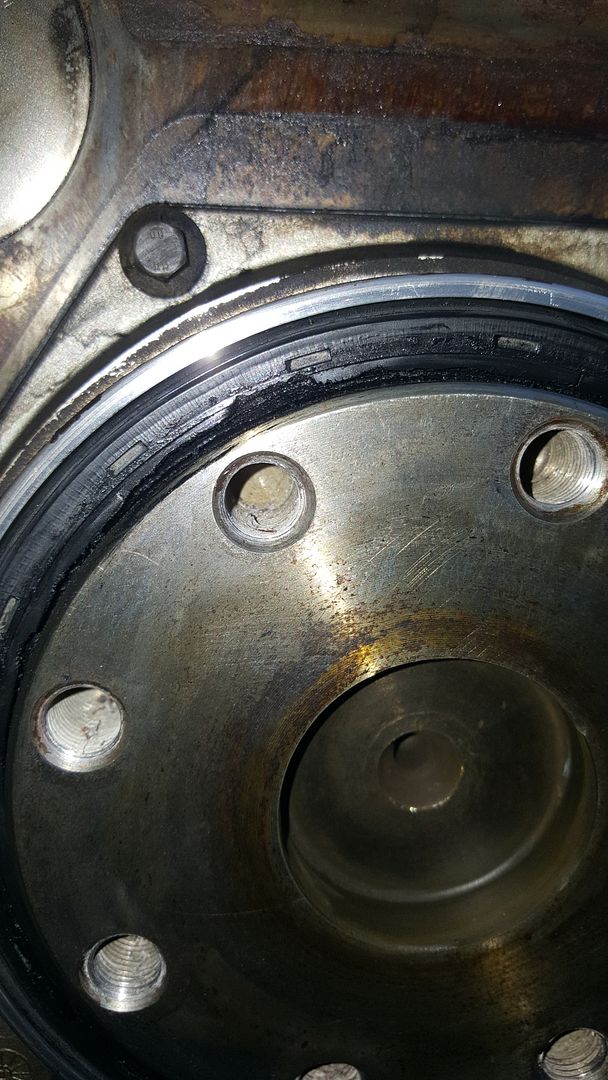
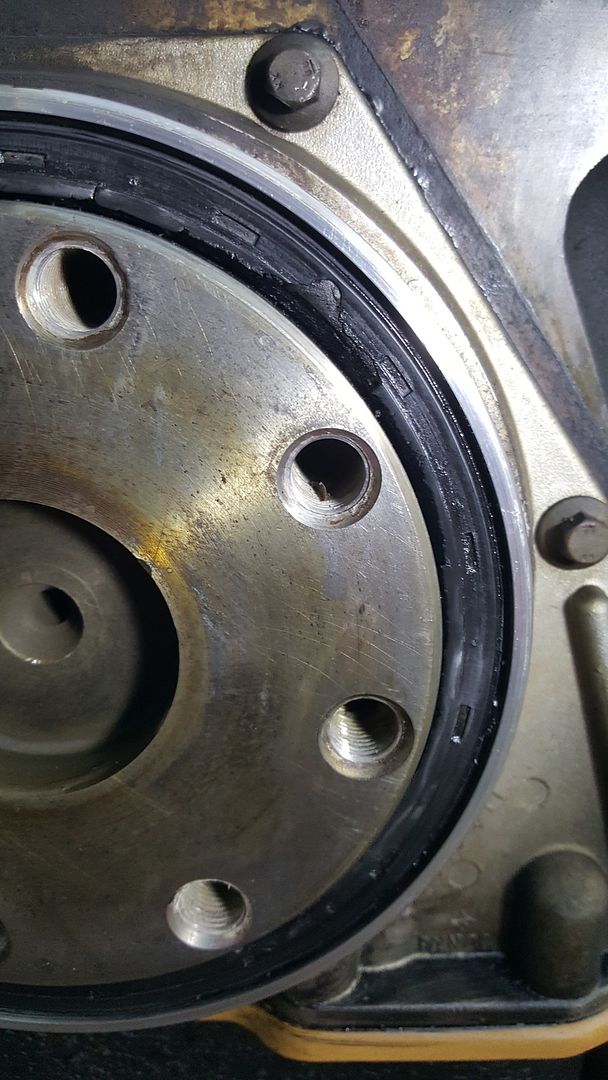
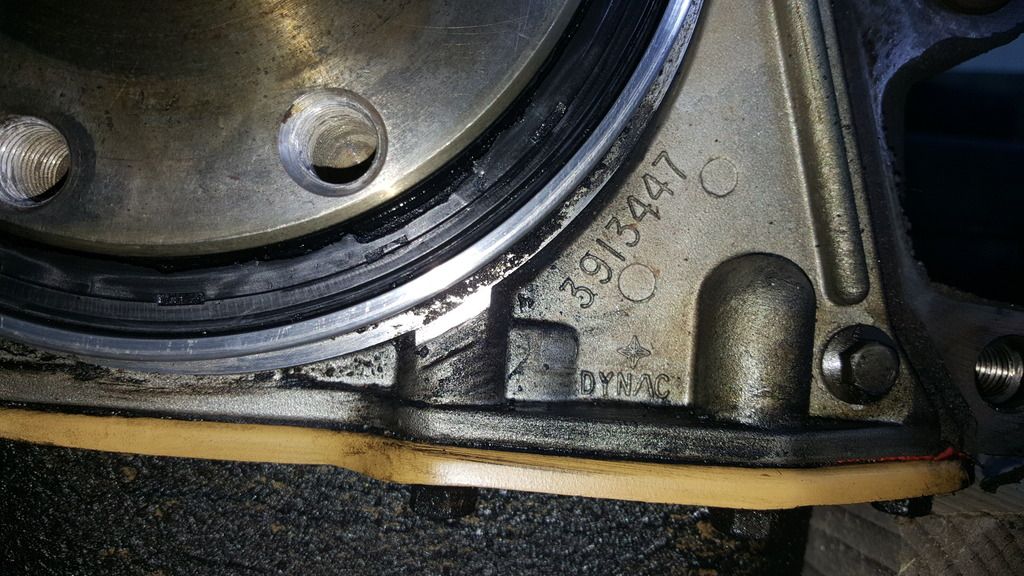
While not the proper way to check piston protrusion but it gives an estimate. Hamilton says for their cams to be truly bolt-in, piston protrusion cannot exceed .018". Since I don't have the dial gauge for checking protrusion, I'll lay a straight edge across the piston crown and check protrusion with feeler gauges to get a closer estimate.
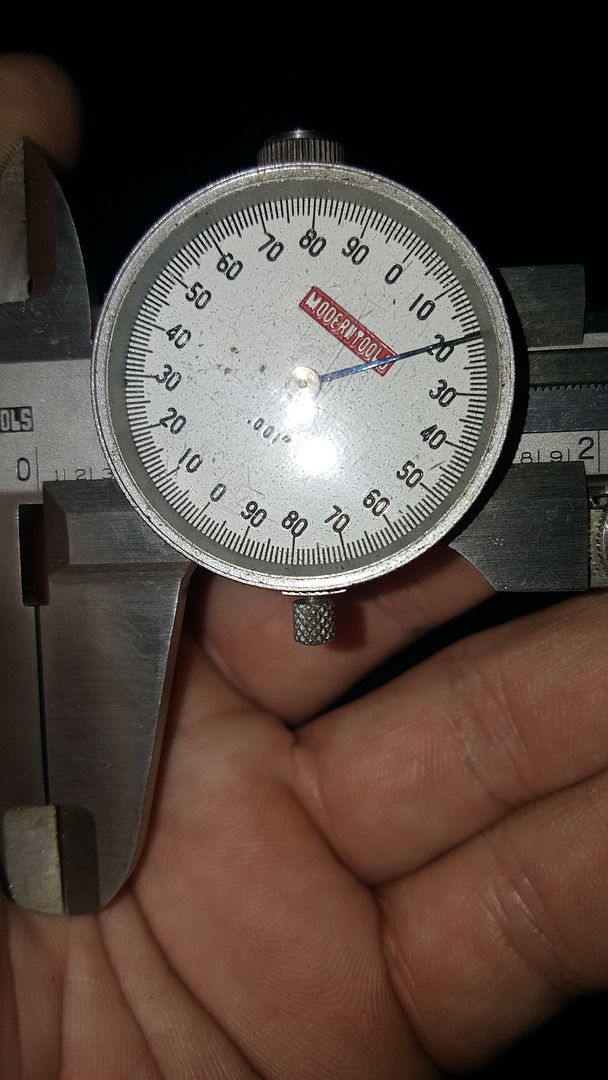
Last edited: