zachu812
New member
I used an LM741 to amplify the signal coming out of the pump sensor and AC coupled the amplified output into a zero crossing ASIC that’s made to read VR sensors, the output is in the pic below.
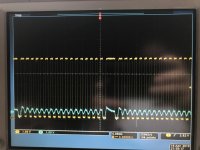
That’s exactly what I’ve been after from the start, I believe this is a signal I can process consistently. Only issue is that the ASIC I’m using is hard to come by. I should’ve ordered a few of those ASICs Brandon mentioned on the first page, now that I have a handle on what’s going on I see why it was recommend so thanks for that :Cheer: Learned a few things along the way so I’ve got some ideas on how to improve upon what I’ve got now, just need parts for it.
Also put together a basic low side driver circuit for the fuel solenoid with a fly back diode across the output. Seems to control it easily, I’m able to pwm the solenoid relatively fast, we’ll see if it’s accurate enough. I’ll have to do some testing to make sure there’s no issues with heat long term.
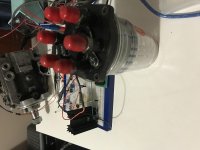
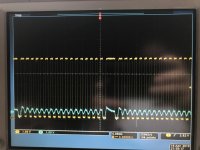
That’s exactly what I’ve been after from the start, I believe this is a signal I can process consistently. Only issue is that the ASIC I’m using is hard to come by. I should’ve ordered a few of those ASICs Brandon mentioned on the first page, now that I have a handle on what’s going on I see why it was recommend so thanks for that :Cheer: Learned a few things along the way so I’ve got some ideas on how to improve upon what I’ve got now, just need parts for it.
Also put together a basic low side driver circuit for the fuel solenoid with a fly back diode across the output. Seems to control it easily, I’m able to pwm the solenoid relatively fast, we’ll see if it’s accurate enough. I’ll have to do some testing to make sure there’s no issues with heat long term.
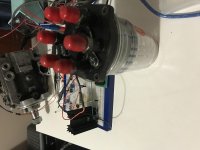