ahale2772
New member
Starting a PPump 24V build on my fathers 02, tow package 2500 HO 6speed truck.
truck is super clean (for a NE truck), 2nd owner, about 150k miles.
the 3rd VP died the other day, no codes, dead pedal and randomly shutting off. its a bluechip pump and a newer APPS.
Went to NH last night and picked up 2 complete 175 hp 12V engines, came out of fedex trucks. one will he scavenged for parts, one kept as a complete spare engine.
first thing we did today was check and make sure his block was a non-53 block, to see if it would be worth the time invested into the 24V swap. its not, so first call was to Gary at Scheid. ordered their .093 mild lines, spacer for the intake, and cam sensor bracket. Also got a set of their 100horse injectors set to p7100 pop, a 2095 rack plug for the pump, and a set of 5k springs. also planning to get a hold or Zack/Ryan at Hamilton and order a cam. plan is to grab a cam that will include the lift pump lobe and use a mechanical piston type lift pump.
goal for the truck is reliability and a clean towing setup. nothing huge HP but a cool 350 hp would be perfect, with egts and boost in check. Need to try and get the MPG's back to where the VP44 was
may need a clutch after its all done, but we will cross that bridge when we get there.
progress should be quick, parts are mostly ordered, and the truck is dead (need it back!). I will try and document as much as we can. biggest mysteries will be trying to use the 12V tappet cover and breather, and figuring out how to best mount the computer. Also need to rig the exhaust brake switch back up on the ppump linkage, and throw a new set of guages at it.
truck is super clean (for a NE truck), 2nd owner, about 150k miles.
the 3rd VP died the other day, no codes, dead pedal and randomly shutting off. its a bluechip pump and a newer APPS.
Went to NH last night and picked up 2 complete 175 hp 12V engines, came out of fedex trucks. one will he scavenged for parts, one kept as a complete spare engine.
first thing we did today was check and make sure his block was a non-53 block, to see if it would be worth the time invested into the 24V swap. its not, so first call was to Gary at Scheid. ordered their .093 mild lines, spacer for the intake, and cam sensor bracket. Also got a set of their 100horse injectors set to p7100 pop, a 2095 rack plug for the pump, and a set of 5k springs. also planning to get a hold or Zack/Ryan at Hamilton and order a cam. plan is to grab a cam that will include the lift pump lobe and use a mechanical piston type lift pump.
goal for the truck is reliability and a clean towing setup. nothing huge HP but a cool 350 hp would be perfect, with egts and boost in check. Need to try and get the MPG's back to where the VP44 was
may need a clutch after its all done, but we will cross that bridge when we get there.
progress should be quick, parts are mostly ordered, and the truck is dead (need it back!). I will try and document as much as we can. biggest mysteries will be trying to use the 12V tappet cover and breather, and figuring out how to best mount the computer. Also need to rig the exhaust brake switch back up on the ppump linkage, and throw a new set of guages at it.
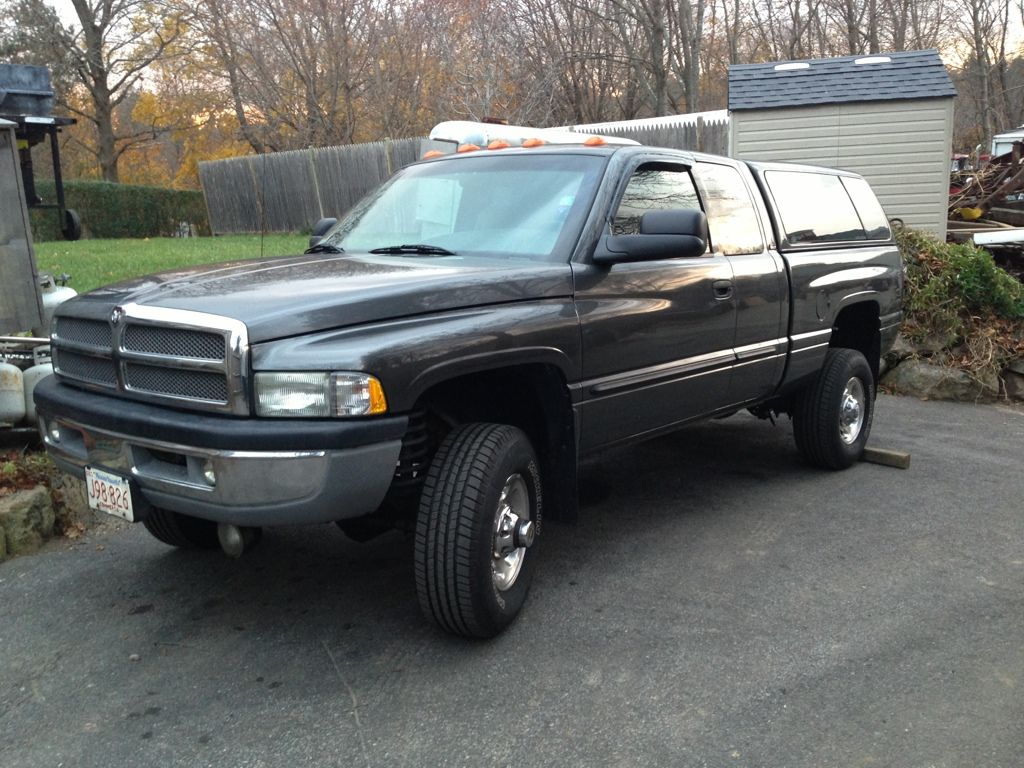
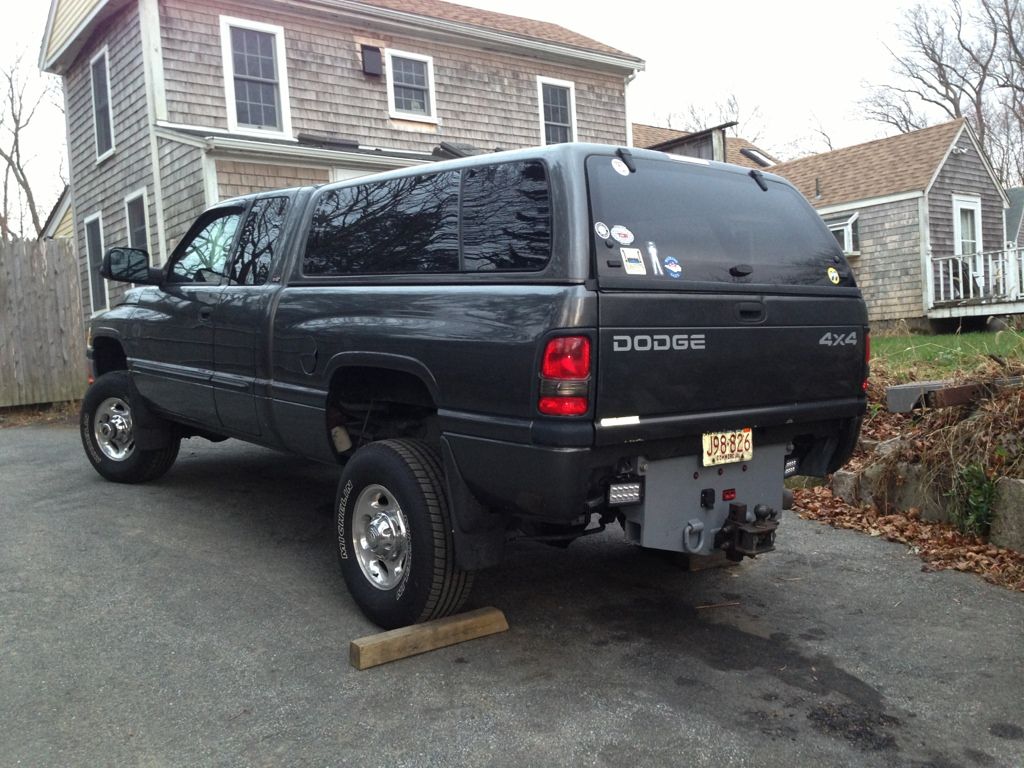
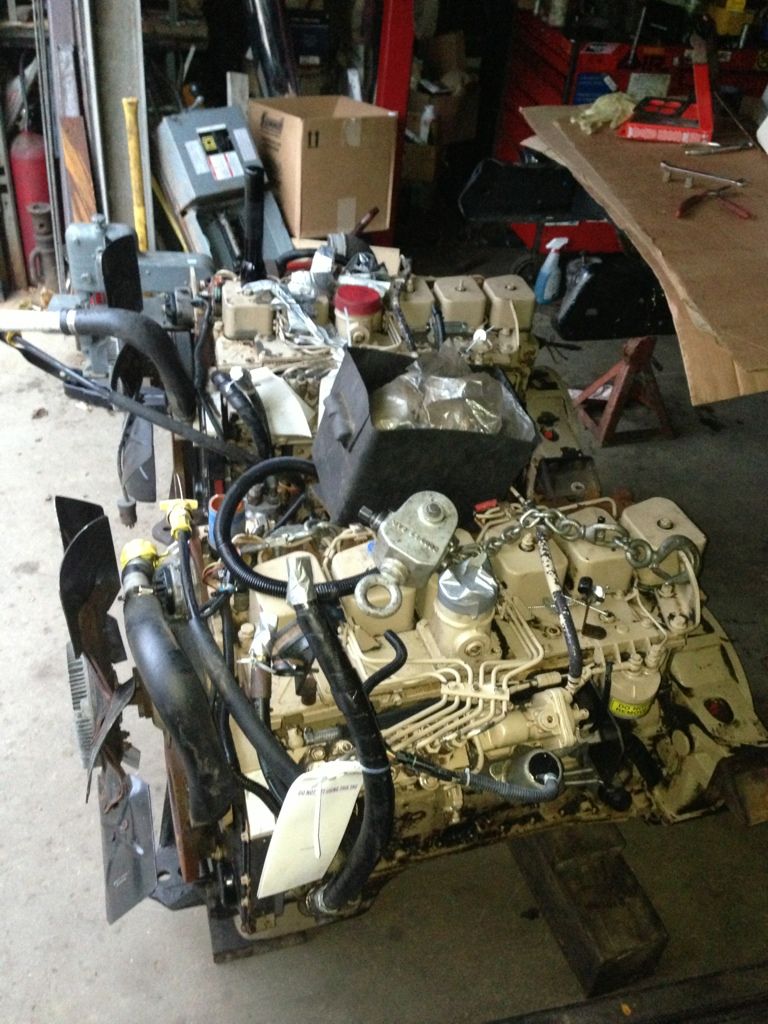