BottleFed
New member
Well i broke the drivers side rear axle shaft last night. Its a dually Dana 80 with the Shied 37 spline axle shafts. Needlesss to say i wont be able to get one before tomorrow night for the last pull of the season up here. I searched all over town today trying to find a set of stock axle shafts to throw in and just weld it solid for this one last pull. Turns out five junk yards didnt have a single one.
Decided to try to weld it and see what happened i figure its better than not pulling at all. I figure if it $hits out again im not really out anything. Illl post a few pictures of how we did it let me know what ya'll think. We beveled the ends and put a keeper pin on the lath to keep it dead center. Then heated it to 400 deg. and welded her up good and hot. Wrapped it in a blanket to let it cool and machiened it back to round. Dunno if it will hold i guess we will find out shortly :bang
Decided to try to weld it and see what happened i figure its better than not pulling at all. I figure if it $hits out again im not really out anything. Illl post a few pictures of how we did it let me know what ya'll think. We beveled the ends and put a keeper pin on the lath to keep it dead center. Then heated it to 400 deg. and welded her up good and hot. Wrapped it in a blanket to let it cool and machiened it back to round. Dunno if it will hold i guess we will find out shortly :bang
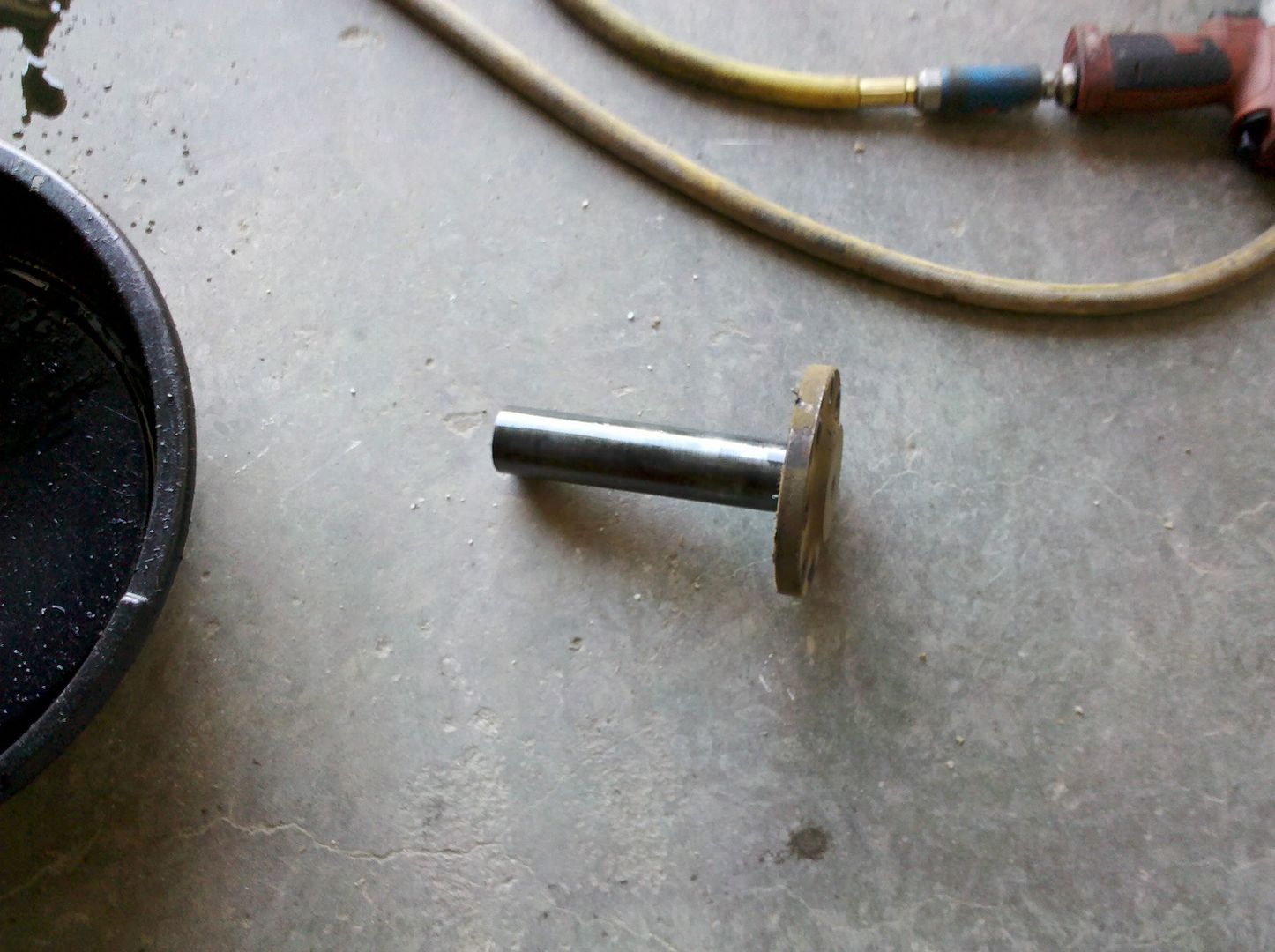
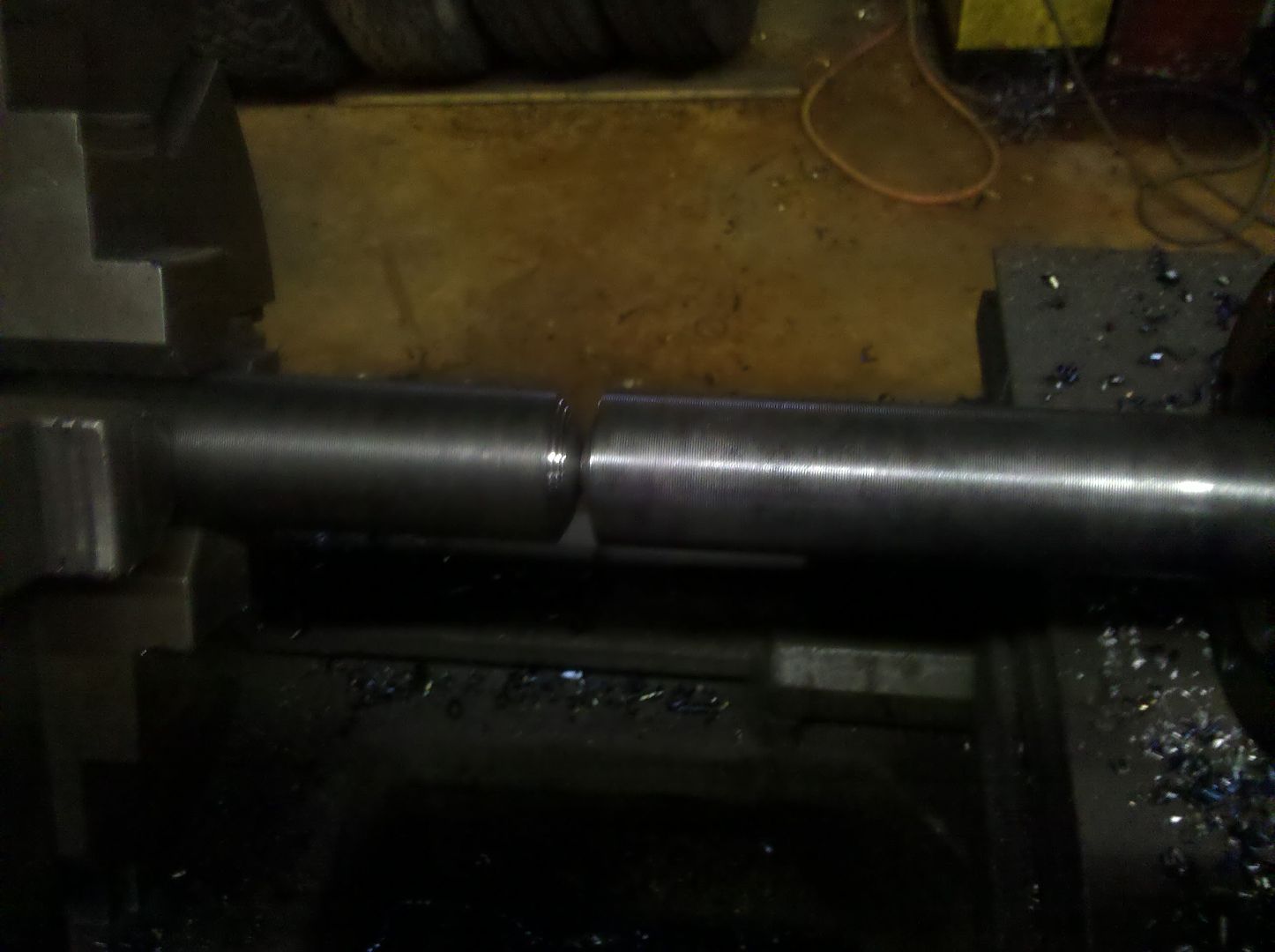
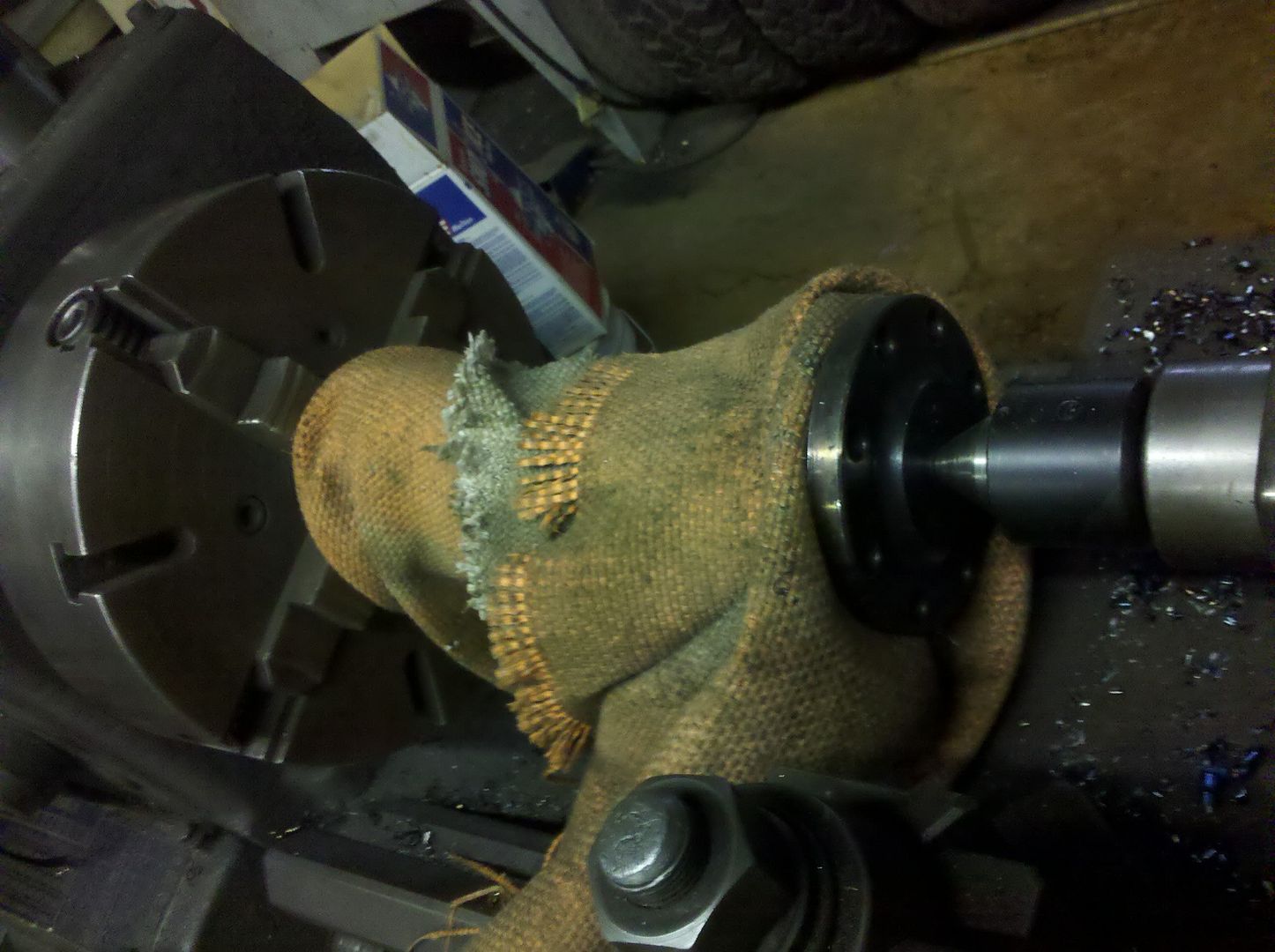
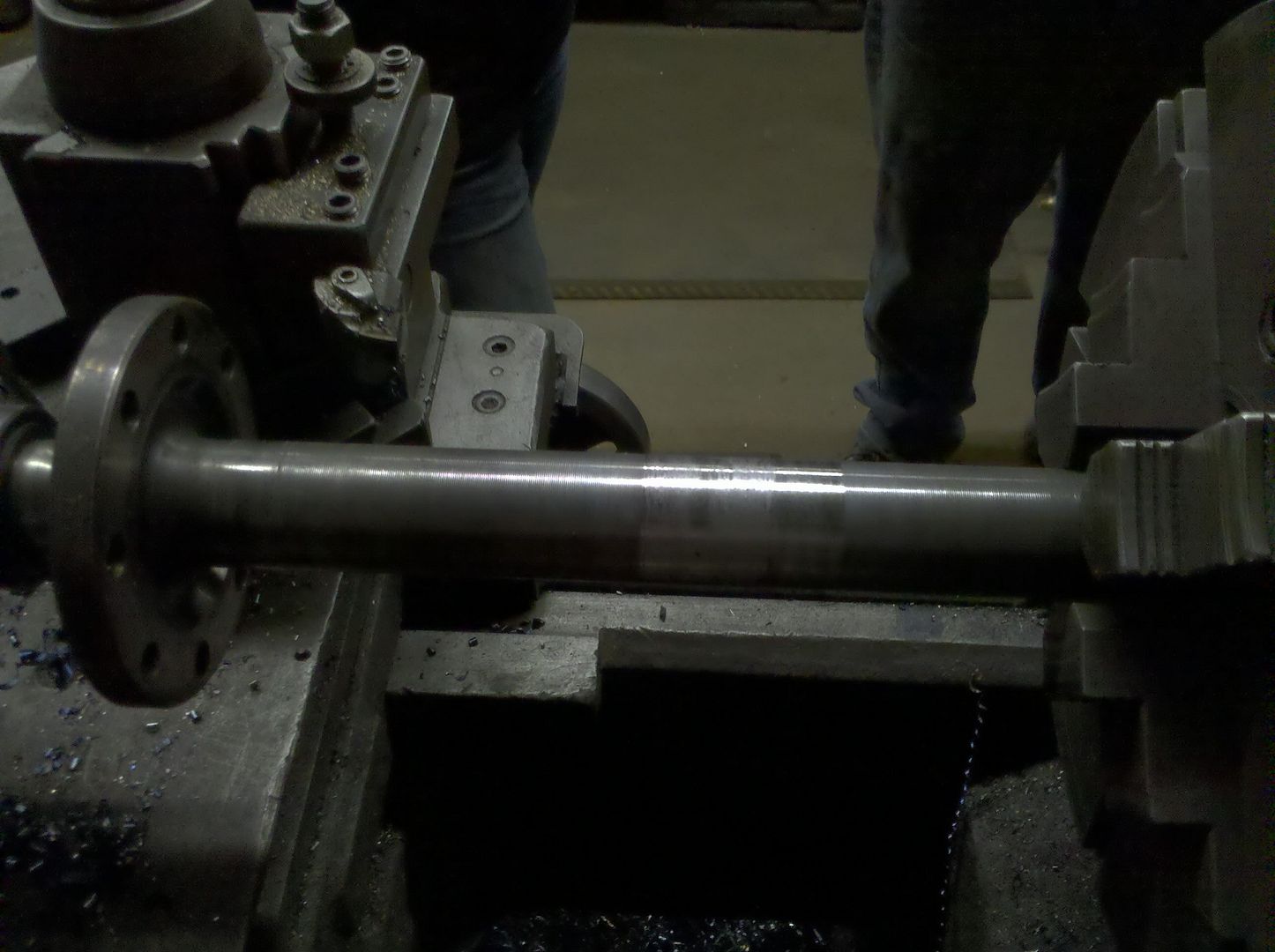