jimbo486
New member
- Joined
- Jan 24, 2010
- Messages
- 1,617
Well, it appears I'll be replacing the head gasket again. Where to start? A new head at least to get rid of this original 9mm injector bore head. Port and polish, valve springs, o-rings, studs...? Dreading it but I've gotta do it.
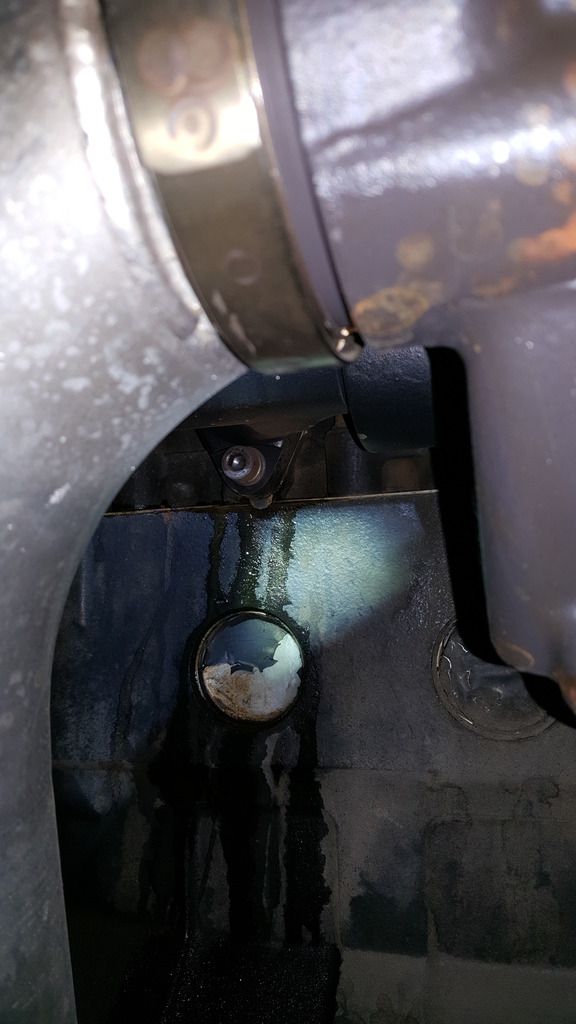
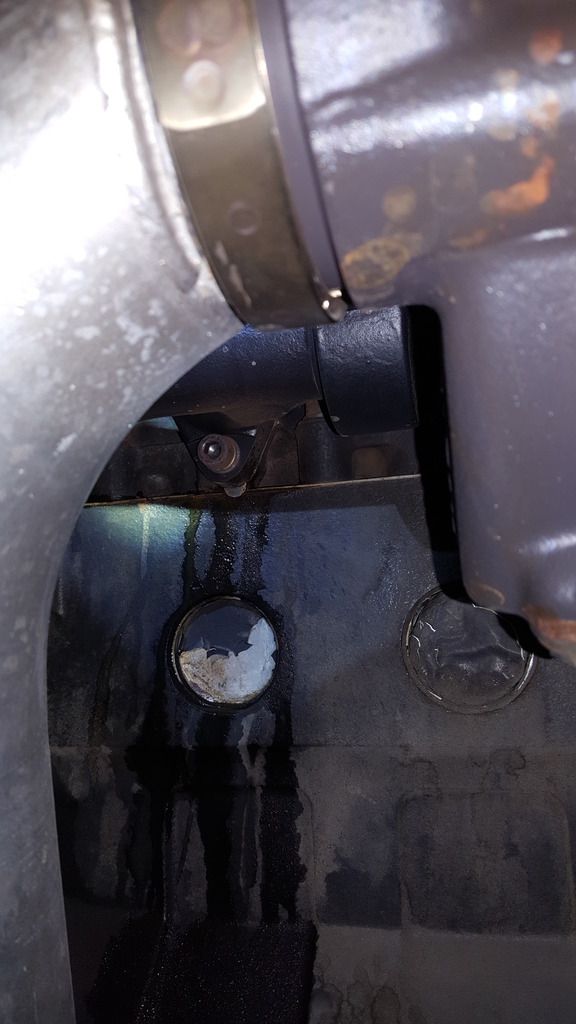
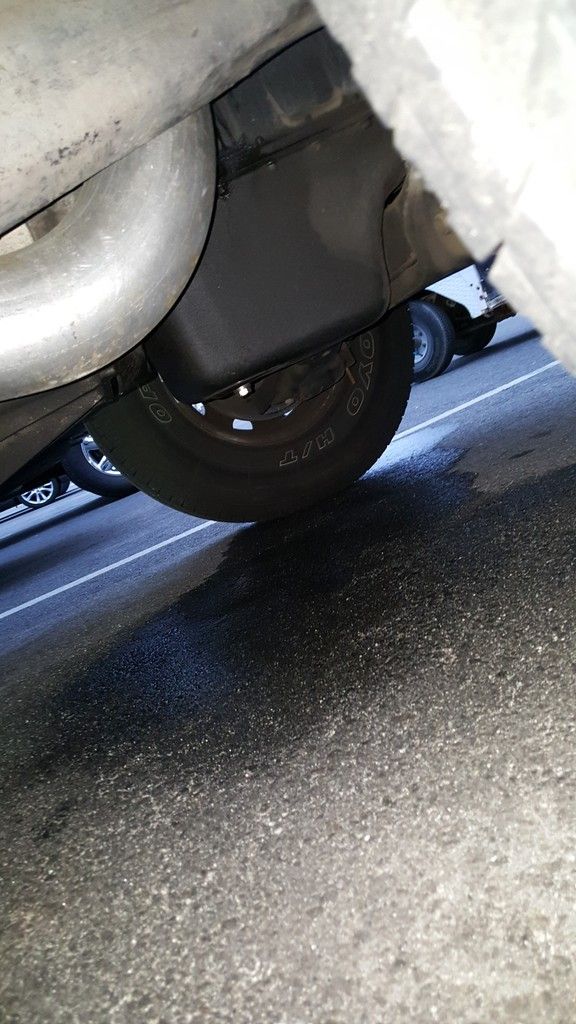
Last edited: