Thekid760
New member
- Joined
- Jun 12, 2008
- Messages
- 475
I found a few older VGT control threads, but they were all closed so I couldn't bump them up. So I figured I'd start a new thread for input on my VGT controller idea.
It isn't a new idea, but a modification on the old boost/dp double acting air cylinder one, modified to try and add and exhaust brake.
Bear with me, it's a little difficult to explain so I also made a diagram.
I like the idea of drive pressure and boost pressure equalizing itself, this seems to me as the most efficient way. But unless you run compressed air I haven't seen any like that with an exhaust brake functional.
As you can see, I have it set up so extending the cylinder will close the housing down and retracting it will open. I will use dp to open the housing and boost to close, hopefully keeping the operation smooth.
I am essentially planning on hooking up a controller that when activated will leave the retract (opening) side open to exhaust, and will switch the dp to the extend side. I figure most EB setups seem to have 40-60psi of dp so I'm hoping that will be enough to keep it closed. I plan on using a larger diameter air cylinder so I can get as much force as possible with only the 40-60 psi.
I have the cylinder mounted in the extend/boost and dp/retract for two main reasons:
- when the dp is forcing it into EB mode, it will be able to take advantage of the full surface area of the piston vs only part of it because of the rod.
- This will also allow me to easily mount a spring over the rod for automatic closing of the housing, and/or return however you want to word it.
The check valves are so I dont put dp into the intake, and I dont create a boost leak when the controller in inactive.
I was talking to BramanteCummins and he brought up that the housing needs to come to rest at a neutral position so as not to load up the engine at idle and off throttle. He mentioned a spring stop that will keep it just out of the EB, but can be overcome by the force of the air cylinder to allow EB.
Thanks for bearing with me, any input will be appreciated.
Clear as mud? :Cheer:
It isn't a new idea, but a modification on the old boost/dp double acting air cylinder one, modified to try and add and exhaust brake.
Bear with me, it's a little difficult to explain so I also made a diagram.
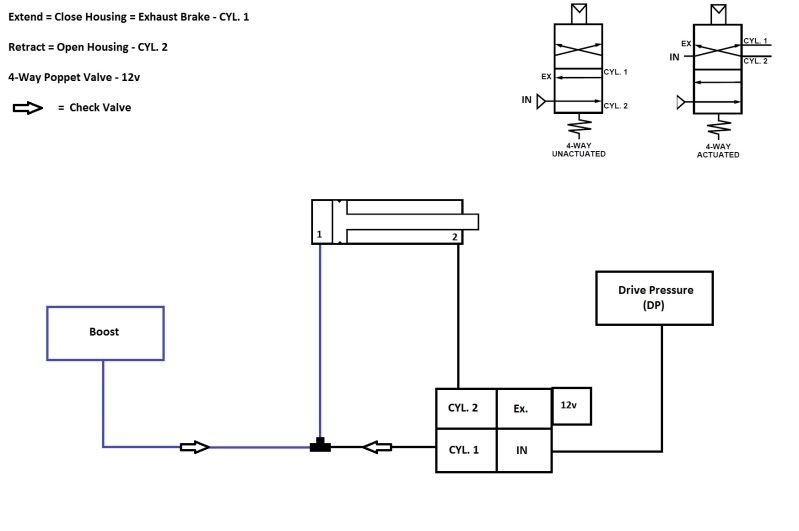
I like the idea of drive pressure and boost pressure equalizing itself, this seems to me as the most efficient way. But unless you run compressed air I haven't seen any like that with an exhaust brake functional.
As you can see, I have it set up so extending the cylinder will close the housing down and retracting it will open. I will use dp to open the housing and boost to close, hopefully keeping the operation smooth.
I am essentially planning on hooking up a controller that when activated will leave the retract (opening) side open to exhaust, and will switch the dp to the extend side. I figure most EB setups seem to have 40-60psi of dp so I'm hoping that will be enough to keep it closed. I plan on using a larger diameter air cylinder so I can get as much force as possible with only the 40-60 psi.
I have the cylinder mounted in the extend/boost and dp/retract for two main reasons:
- when the dp is forcing it into EB mode, it will be able to take advantage of the full surface area of the piston vs only part of it because of the rod.
- This will also allow me to easily mount a spring over the rod for automatic closing of the housing, and/or return however you want to word it.
The check valves are so I dont put dp into the intake, and I dont create a boost leak when the controller in inactive.
I was talking to BramanteCummins and he brought up that the housing needs to come to rest at a neutral position so as not to load up the engine at idle and off throttle. He mentioned a spring stop that will keep it just out of the EB, but can be overcome by the force of the air cylinder to allow EB.
Thanks for bearing with me, any input will be appreciated.
Clear as mud? :Cheer: