XLR8R
Crew Chief
- Joined
- Sep 10, 2007
- Messages
- 2,364
Saw pix of this before somewhere - searched to no avail.
These are from what I'm currently wrenching on:
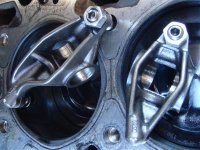
Rocker arms have some galling on the pressure side.

Trunnions exhibit similiar features, wear on pressure side is right at .001"
What's acceptable wear on these?
Won't polishing the rocker bores and trunnion ODs to remove the galling be fine, especially in addition to HPC-coating the trunnions?
All rockers & trunnions show more wear on their rearward side than the front - any ideas as to the cause of this phenomenom?
These are from what I'm currently wrenching on:
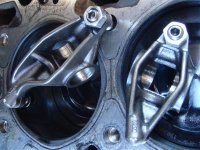
Rocker arms have some galling on the pressure side.

Trunnions exhibit similiar features, wear on pressure side is right at .001"
What's acceptable wear on these?
Won't polishing the rocker bores and trunnion ODs to remove the galling be fine, especially in addition to HPC-coating the trunnions?
All rockers & trunnions show more wear on their rearward side than the front - any ideas as to the cause of this phenomenom?